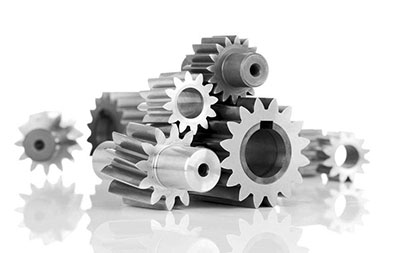
直伞齿轮在安装过程中有哪些问题是需要注意的
一、轴线共面性:安装基础的关键
1.轴线偏差的危害
若两轴中心线未调整至同一平面,会导致齿轮啮合不均匀,部分齿面承受过大压力,加速磨损,甚至引发设备振动和噪音。例如,某机械厂曾因未检查轴线共面性,导致伞齿轮在运行3个月后出现齿面点蚀,维修成本增加2万元。
2.调整方法
专业工具测量:使用经纬仪、水准仪或塞杆法(将两根塞杆插入轴承孔,用测微片检查末端平面距离)精确测量轴线偏差。
直角尺校正:若两轴交角为90°,需用直角尺检查垂直度,确保轴线交角准确。
二、间隙精度:影响传动平稳性的核心参数
1.间隙过大的风险
啮合间隙过大会导致齿轮运转时产生冲击,牙齿易打坏。例如,某汽车变速箱因伞齿轮间隙超标(0.2mm),在高速换挡时出现齿轮断裂事故。
2.间隙过小的危害
间隙过小则可能卡死设备。某印刷机厂商曾因未调整伞齿轮间隙,导致设备启动时电机烧毁,直接损失达5万元。
3.调整方法
增减垫片:通过改变垫片厚度调节间隙,标准值为0.08-0.15mm。
铅丝法检测:将铅丝压入齿面啮合处,测量压扁后的厚度以确定间隙。
百分表测量:固定主动轮,用百分表测从动轮轴向窜动量,标准值≤0.03mm。
三、接触斑点:判断啮合质量的直观指标
1.合格标准
位置:接触斑点应位于齿面中部,偏向小头一侧2-4mm。
面积:斑点面积占比≥60%。
2.调整方法
红丹粉涂色:在主动轮齿面涂红丹粉,手动转动齿轮副3-5圈,观察从动轮齿面接触情况。
修正中心距:若斑点偏齿顶或齿根,需调整垫片厚度修正中心距,每次增减量建议0.02mm。
四、螺栓紧固:确保连接可靠性的关键环节
1.紧固规范
高强度螺栓:使用8.8级以上螺栓,分三次交叉拧紧(预紧至30%、80%、100%额定扭矩)。
扭矩控制:例如M12螺栓按98N·m标准执行,每次拧紧后标记螺栓位置,防止漏拧。
2.法兰连接检查
用0.02mm塞尺检查法兰连接处,确保塞尺无法插入,防止漏油或松动。
五、安全防护:避免人身与设备损伤的底线
1.加热操作规范
温度控制:过盈配合齿轮需加热至80-100℃,并在5分钟内完成安装,防止温度过高导致齿轮变形。
防护措施:加热时戴石棉手套,严禁用氧气枪局部加热,避免烫伤或齿轮爆裂。
2.调试安全要求
旋转方向避让:调试时身体避开齿轮旋转切线方向,长发者必须盘入工作帽。
润滑剂处理:润滑剂沾染皮肤立即用皂液清洗,废油收集需符合GB/T17145标准。
六、其他注意事项
1.清洁与预处理
用煤油或专用清洗剂清洗齿轮内孔和轴颈,去除防锈油和杂质。
测量轴颈和齿轮内孔尺寸,过盈配合需加热,间隙配合涂抹二硫化钼润滑脂。
2.试运行监控
空载运行:初次启动转速控制在额定值25%,运行10分钟后停机检查温升和振动。
负载测试:从30%载荷逐步增加,用红外测温枪监测轴承温度(不超过70℃)。
3.长期停用维护
齿面涂抹食品级润滑脂并包裹防潮纸,防止锈蚀。
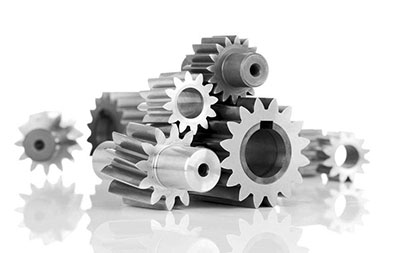
非标齿轮具体是什么
非标齿轮的“非标”主要体现在尺寸参数或齿形结构上不符合标准齿轮的规定。例如,模数、齿数、齿形角、齿顶高系数、顶隙系数等参数可能超出标准范围,或者齿形、齿宽、齿轮外径等尺寸有特殊要求。这些特殊要求通常源于特定的传动需求或安装条件。
与标准齿轮的区别
尺寸参数:标准齿轮的尺寸参数严格遵循国家标准或行业标准,如模数可能为1mm、1.25mm、1.5mm等标准值,齿数也通常在标准系列内选取。而非标齿轮的尺寸参数则可能超出这些标准范围,如模数为2.2mm、齿数为43的齿轮就属于非标准件。
齿形结构:标准齿轮通常具有标准的齿形,如渐开线齿形,并且结构较为常规。非标齿轮则可能具有特殊的齿形,如摆线齿形、圆弧齿形等,或者在结构上有特殊设计,如带有轮毂、键槽、安装孔等,以满足特定的安装和传动要求。
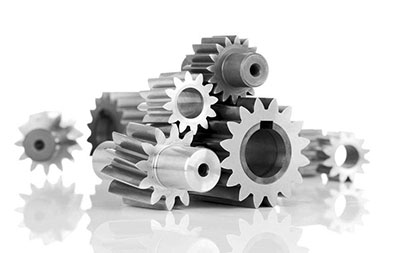
平面直伞齿轮的设计基准有哪些
平面直伞齿轮的设计基准涵盖分度圆锥、基准孔(内孔)、端面、齿顶圆及中心孔,这些基准共同确保齿轮的加工精度、装配稳定性及传动性能。以下为具体说明:
1.分度圆锥:分度圆锥是伞齿轮设计中最核心的基准。它决定了齿轮的齿数、模数、压力角等关键参数,是齿轮传动比和几何尺寸计算的基础。分度圆锥的精度直接影响齿轮的啮合性能和传动效率。
2.基准孔(内孔):在齿轮的加工、检验和安装过程中,内孔常作为定位基准。它要求较高的精度,通常采用7级精度并遵循包容原则,以确保齿轮在装配时的准确性和稳定性。
3.端面:齿坯两端面是切齿加工时的重要定位基准。为保证切齿精度,需规定两端面相对于基准孔轴线的端面径向圆跳动公差,如某些设计中要求该公差为0.016mm或0.008mm。
4.齿顶圆:齿顶圆在某些设计中也作为加工及测量基准。此时,需规定齿顶圆的尺寸公差(如IT8级)、圆柱度公差以及对基准孔轴线的径向圆跳动公差,以确保齿轮的几何形状和位置精度。
5.中心孔:在齿轮的设计和加工中,中心孔也常作为基准。它用于确定齿轮的轴向位置和径向位置,确保齿轮在装配时的准确性和稳定性。
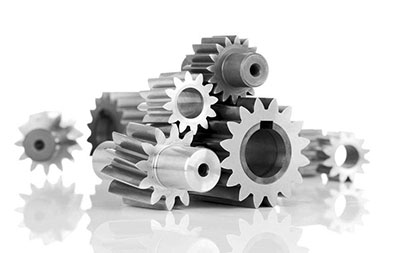
直伞齿轮的加工技术及注意事项
直伞齿轮,也称为直齿锥齿轮,是机械传动中常用的一种齿轮类型。它们主要用于两轴相交的传动,特别是在空间布局受限的情况下,直伞齿轮能够实现空间角度的转换,使得动力传输更加灵活高效。本文将为您详细介绍直伞齿轮的加工技术、材料选择、应用领域以及加工时需要注意的事项。
一、直伞齿轮的加工技术
直伞齿轮的加工技术主要包括成形法和展成法两种。成形法是通过特定形状的刀具直接切削出齿轮的齿形,这种方法适用于小批量生产;而展成法则是一种基于齿轮啮合原理的加工方法,它利用一对齿轮的啮合运动来切削出齿轮的齿形,这种方法精度高,适合大批量生产。
1. 成形法:使用特定形状的刀具直接在齿轮毛坯上切削出所需的齿形。这种方法操作简单,但精度和效率相对较低。
2. 展成法:通过一对齿轮的啮合运动来加工齿轮,能够实现高精度的齿形加工。展成法又分为滚切法和磨削法,其中滚切法适用于软材料的初步加工,而磨削法则适用于硬材料的精加工。
二、材料选择
直伞齿轮的材料选择需考虑齿轮的工作条件,如载荷大小、速度、工作环境等。常用的材料包括:
钢:如45#钢、20CrMnTi等,适用于中等负荷和速度的场合。
铸铁:如HT200,适用于低速、重载的场合。
非金属材料:如尼龙、聚甲醛等,适用于低速、轻载的场合,具有良好的自润滑性能。
三、应用领域
直伞齿轮因其独特的传动特性,广泛应用于汽车、航空航天、机床、船舶等多个领域。例如,在汽车变速箱中,直伞齿轮用于实现前后轮驱动的转换;在航空航天领域,用于调整发动机和螺旋桨之间的角度;在机床和船舶中,用于实现空间角度的转换,提高机械传动的灵活性。
四、加工时需要注意的事项
1. 精度要求:直伞齿轮的加工精度直接影响到齿轮的使用寿命和传动效率,因此在加工过程中需严格控制齿形、齿距等参数的误差。
2. 材料处理:对于硬度较高的材料,加工前应进行适当的热处理,以提高材料的加工性能。
3. 冷却与润滑:加工过程中应使用适当的冷却液和润滑剂,以减少刀具磨损,提高加工效率。
4. 安全操作:操作人员需接受专业培训,严格遵守操作规程,确保加工过程的安全。
总之,直伞齿轮作为一种重要的机械传动部件,其加工技术的不断进步对于提高机械设备的性能具有重要意义。选择合适的材料、采用先进的加工技术和严格的质量控制是保证直伞齿轮性能的关键。
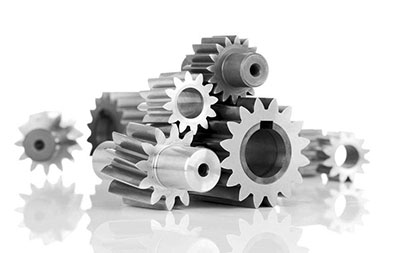